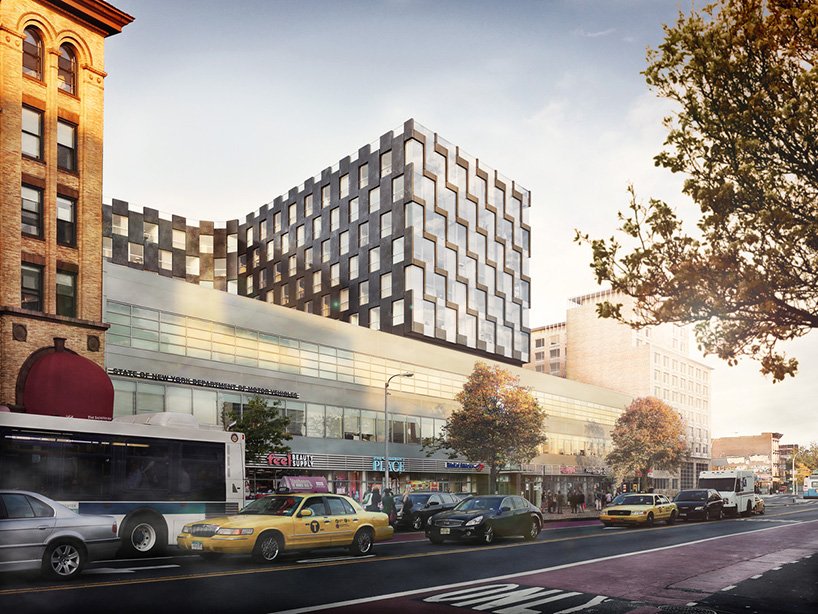
What are the types of WPC?
1. Single-Screw Extruder - A single-screw fiber composite extruder is the simplest extrusion system for producing WPC profiles. A typical single-screw extruder will have a barrel length to diameter (L/D) ratio of 34:1. It will employ two stages, melting and metering, and a vent section to remove volatiles. The material form for the single-screw extruder will be pre-compounded fiber-filled polymer pellets. A dryer may also be required to dry the pellets. The material feed method is usually by gravity hopper. The melting/mixing mechanism is barrel heat and screw shear. Advantages of the single-screw extruder are that it is a proven technology and this method has the lowest capital acquisition cost. Disadvantages include high raw material cost, lower output rates, drying system required, polymer is melted with the fiber with greater risk of fiber thermal decomposition, high screw speed (rpm) with greater risk of burning at the screw tip, and inability to keep melt temperature low with higher head pressures.
2. Counter-Rotating Twin-Screw Extrusion - Counter-rotating twin-screw extruders excel in applications where heat-sensitive polymers like rigid polyvinyl chloride (PVC) are utilized, low temperature extrusion for fibers and foams, non-compounded materials like powder blends, materials that are difficult to feed, and those materials that require degassing. The counter-rotating twin screw can either have parallel or conical screw configurations. The fiber/flour and polymer are in the same polymer size, usually 250 to 400 μm. Material preparation includes fiber drying followed by high-intensity blending with the polymer and additives. The material feed method usually utilizes a crammer feeder. The melting/mixing mechanism is barrel heat and screw mixing. Screw mixing is accomplished through screw flight cut-outs and gear mixers. Moisture removal is through vacuum venting. Advantages of counter-rotating twin-screw extrusion include its low screw speed (rpm) and low shear mixing, and it is a proven technology. Disadvantages include that a drying system is required, a size reduction system for fed materials may be necessary, a pre-blending system is required, and material transportation can impact the mix feed ratios.
3. Co-rotating Twin-Screw and Hot Melt Single-Screw Wood Composite System - A co-rotating twin screw in combination with a hot melt single screw can be used to produce wood–plastic composite profiles. In this case, a parallel 40:1 L/D co-rotating twin-screw extruder is coupled with a hot melt 10:1 L/D, single-screw extruder. The material for this system is wood flour or fiber at ambient moisture content (5 to 8 %), and the polymer and additives can be in their natural states. No material preparation is required in terms of pre-blending components. The preferred material feed systems are gravimetric feeders and twin-screw side feeders. The melting/mixing mechanism includes barrel heat, screw speed (rpm), and screw mixing. Moisture removal is accomplished through the use of atmospheric and vacuum vents. Advantages of this system include the ability to process wood at ambient moisture content since the extruder is used to dry the fiber with the elimination of drying and pre-blending operations, and good fiber/polymer mixing. Disadvantages include the need for peripheral feeding systems, high screw speed (rpm) and no screw cooling (greater risk of burning), inability to keep melt temperature low with higher head pressures, and polymer is still melted with the fiber (greater risk of burning, more difficult to vent).
4. Woodtruder™ - The Woodtruder™ includes a parallel 28:1 L/D counter-rotating twin- and a 75-mm single-screw extruder, a blending unit, a computerized blender-control system, a die tooling system, a spray cooling tank with driven rollers, a traveling cut-off saw, and a run-off table. As processing begins, ambient moisture content wood flour is placed into the unit’s fiber feeder and dried within the twin screw. Meanwhile, separate from the fiber, the plastics are melted. The melting/mixing mechanism includes barrel heat and screw mixing. The separation of wood conveying and plastic melting ensures that fibers will not be burned during plastic melting and that the melted plastic will encapsulate the fibers completely. These materials are then mixed, and any remaining moisture or volatiles are removed by vacuum venting. Advantages of this system include that the flour and additives are in their natural states and no material preparation is required. Gravimetric feeders are preferred as the material feed method. Advantages of the Woodtruder™ include the ability to process fiber at ambient moisture content (5 to 8 %), separate melting process of the polymer, good polymer/fiber mixing, screw cooling is included on the twin screw, the ability to maintain a low melt temperature with a high head pressure, superior venting, the elimination of drying, size reduction and separate pre-blending equipment, highly flexible integrated process control system for material feeding, and extruder unit operations. Disadvantages include lower product throughput, higher capital costs, and using the main extruder as a dryer is not the most efficient manner to process dry wood flour.
Chat with us on WhatsApp

Anil Kumar
Sales Manager
Hey there 😃
Need WPC products ?